Mks Melzi V2.0 User Manual Pdf English
Nov 19, 2018 MKS TFT touch screen includes TFT24/28/32/35/70, which can be connected to the motherboard for control via AUX-1. Support Simplified Chinese, Traditional Chinese, English, Russian, Spanish and more than 5 languages, and support online language switching. makerbase-mks/MKS. Marlin Firmware Open Source 3D Printer Driver. First created in 2011 for RepRap and Ultimaker by Erik van der Zalm et. Al., today Marlin drives most of the world's 3D printers.
MKS board is an control board for RepRap Prusa i3 3D compatible printer. This board has integrated Arduino Mega2560 and Ramps1.4 control board and make the circuit installation much simpler than before.
MKS Board has following three sub-version:
User Manual
sub-version | Picture |
MKS Base V1.5 | |
MKS Base V1.4 | |
MKS Gen V1.4 |
MKS Base board integrated 5 servo control model which does not included in MKS Gen 1.4 board. All other features of these two boards are same. We can use same Marlin firmware for both boards.
Please take following steps to install the software in order to let your printer work properly.
Prerequisite:
1) Pls check the intalltion and connection graph link for MKS with 12864 or 2004LCD
2) Pls check the intalltion and connection graph link for MKS with 2.8″ or 3.2″ TFT Touch LCD
(if you don’t know how to connect the circuit yet, check with your supplier or google the related topic).
Please be noted MKS board Z axis servo controller installation as following:
If you have only one Z axis servo, please connect it to Z_MOT slot, if you have two Z axis servos, another servo should be connected to E1_MOT.
For MKS Gen Board:
Instruction Manual
If you have only one Z axis servo, please connect it to Z slot, if you have two Z axis servos, another servo should be connected to E1.
Caution: do not plug or unplug and wire or module when power is on, do not even touch the board when power is on or your hand has static charge(you can rmove static charge by touching metal tap) . Always double check power wire is properly installed. If you do not follow above move, you can damage the control board and your 3D printer.
Step 1) Install Arduino and driver (Please download the Arduino IDE version 1.5.X, you’d better download 1.5.4 version IDE).
First, please download Arduino IDE from https://www.arduino.cc/en/Main/OldSoftwareReleases#previous.
Step 2) use USB cable to connect Arduino Mega2560 and your PC. Your pc should detect Arduino Mega2560 and install driver automatically.
If driver can not be installed automatically, you can download the driver from following link:
Unzip above file and run the installation program
Step 3)Install U8glib library into Arduino IDE. If you have already installed U8glib, please skip this step>
First: Download U8glib library from OSOYOO U8glib library .
Then, in Arduino IDE ->Sketch->Include Library->Add Zip Library , select the zip file you just downloaded and load into IDE. see following picture:
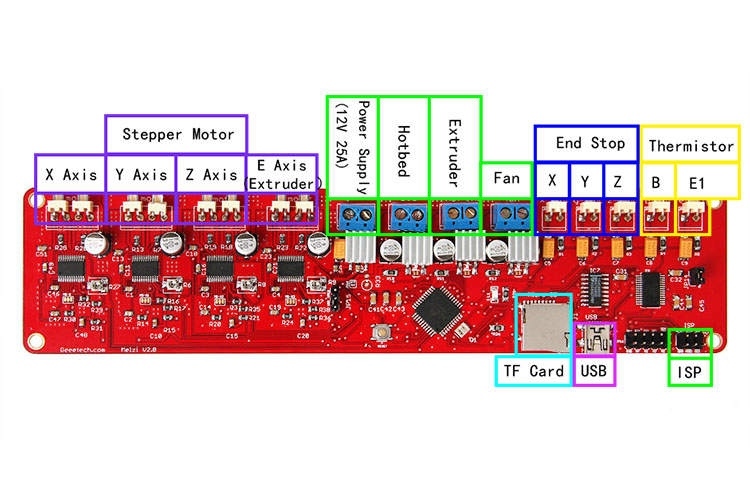
Step 4) In Arduino IDE->Tools->Board select Arduino Mega 2560:
In Tools->Port select the COM port which associated with Arduino Mega2560(see picture below)
Step 5)Download Ramps1.4 board Marlin firmware as per your LCD screen type.
LCD screen No. | Picture | Download link |
2004 LCD | 2004 LCD Marlin firmware | |
12864 LCD | 12864 LCD Marlin firmware | |
2.8″ TFT Touch Screen | 2.8″ TFT touch screen Marlin firmware | |
3.2″ TFT Touch Screen | 3.2″ TFT touch screen Marlin firmware |
Unzip above file, you will see a folder called “Marlin”
In above Marline folder, there is Configuration.h file which defines some important hardware config setting values. Please read following instruction to change the Configuration.h and configuration_adv.h file according to your hardware situation:
A)If you connect MKS Gen/Base board with two Z axis servo motors, please make following changes,
In configuration.h line 248 to 253:
#define INVERT_X_DIR false // for Mendel set to false, for Orca set to true
#define INVERT_Y_DIR true // for Mendel set to true, for Orca set to false
#define INVERT_Z_DIR false // for Mendel set to false, for Orca set to true
#define INVERT_E0_DIR false // for direct drive extruder v9 set to true, for geared extruder set to false
#define INVERT_E1_DIR false // for direct drive extruder v9 set to true, for geared extruder set to false
#define INVERT_E2_DIR false // for direct drive extruder v9 set to true, for geared extruder set to false
in configuration_adv.h uncomment line 148 #define Z_DUAL_STEPPER_DRIVERS as following:
As ever you can get started in seconds by choosing a profile optimised for your device and navigating this easy to use interface.Key features include:. Title and chapter selection. Integrated bitrate calculator. Handbrake 1.0.7 manual download. Its latest version was launched in late 2018 and comes with a wealth of updates and fixed issues. Subtitle support (VobSub Closed Captions CCEA-608, SSA, SRT).
#define Z_DUAL_STEPPER_DRIVERS // disable this line if you have only one Z motor
B)If you connect MKS Gen/Base board with only One Z axis servo motors, please make following changes,
In configuration.h line 248 to 253:
#define INVERT_X_DIR false // for Mendel set to false, for Orca set to true
#define INVERT_Y_DIR true // for Mendel set to true, for Orca set to false
#define INVERT_Z_DIR false // for Mendel set to false, for Orca set to true
#define INVERT_E0_DIR false // for direct drive extruder v9 set to true, for geared extruder set to false
#define INVERT_E1_DIR false // for direct drive extruder v9 set to true, for geared extruder set to false
#define INVERT_E2_DIR false // for direct drive extruder v9 set to true, for geared extruder set to false
in configuration_adv.h disable line 148 #define Z_DUAL_STEPPER_DRIVERS as following:
//#define Z_DUAL_STEPPER_DRIVERS // disable this line if you have only one Z motor
Step 6)In Arduino IDE->File->Open, find Marlin Folder and open Marlin Arduino File(Marlin.ino)
Your IDE will compile the firmware and load it into Mega2560 board. There might be some warning error message during compiling, just neglect those message.
After the firmware is loaded into Arduino Mega2560, your LCD will show 3D printer menu as per following picture:
Now you can now control the printer accordingly.
Details
The Arduino CNC Shield makes it easy to get your CNC projects up and running in a few hours.
It uses opensource firmware on Arduino to control 4 stepper motors using 4 A4988 Stepper drivers, with this shield and the Arduino you can build all kinds of robotics or CNC projects including CNC routers, laser cutters and even pick&place machines.
- Arduino CNC Shield Version 3
- GRBL 0.9 compatible. (Open source firmware that runs on an Arduino UNO that turns G-code commands into stepper signalshttps://github.com/grbl/grbl)
- 4-Axis support (X, Y, Z , A-Can duplicate X,Y,Z or do a full 4th axis with custom firmware using pins D12 and D13)
- 2 x End stops for each axis (6 in total)
- Coolant enable
- Uses removable Pololu A4988 compatible stepper drivers. (A4988, DRV8825 and others)(Not Included)
- Jumpers to set the Micro-Stepping for the stepper drivers. (Some drivers like the DRV8825 can do up to 1/32 micro-stepping )
- Compact design.
- Stepper Motors can be connected with 4 pin molex connectors or soldered in place. .
- Runs on 12-36V DC. (At the moment only the Pololu DRV8825 drivers can handle up to 36V so please consider the operation voltage when powering the board.)
Mks Melzi V2.0 User Manual Pdf English Lessons
Description
This expansion board as a driver expansion board, can be used for engraving machines, 3D printers
It is a total of four slots, can drive four A4988 stepper motor. Each road stepper motors only need two IO ports. In other words, six IO ports can be well managed three stepper motors
IO corresponding figure above
UNO for Arduino---------------------- expansion board
8 ------------------------ EN ( stepper motor driver enable , active low )
7 ----------------------- Z.DIR (Z -axis direction control )
6 ----------------------- Y.DIR (Y -axis direction control )
5 ----------------------- X.DIR (X -axis direction control )
4 ---------------------- Z.STEP (Z -axis stepper control )
3 ---------------------- Y.STEP (Y -axis stepper control )
2 ---------------------- X.STEP (X -axis stepper control )
/ / The following is a simple stepper motor control procedures,
# define EN 8 / / stepper motor enable , active low
# define X_DIR 5 / / X -axis stepper motor direction control
# define Y_DIR 6 / / y -axis stepper motor direction control
# define Z_DIR 7 / / z axis stepper motor direction control
# define X_STP 2 / / x -axis stepper control
# define Y_STP 3 / / y -axis stepper control
# define Z_STP 4 / / z -axis stepper control
/ *
/ / Function : step . function: to control the direction of the stepper motor , the number of steps .
/ / Parameters : dir direction control , dirPin corresponding stepper motor DIR pin , stepperPin corresponding stepper motor ' step ' pin , Step number of step of no return value.
* /
void step (boolean dir, byte dirPin, byte stepperPin, int steps)
{
digitalWrite (dirPin, dir);
delay (50);
for (int i = 0; i digitalWrite (stepperPin, HIGH);
delayMicroseconds (800);
digitalWrite (stepperPin, LOW);
delayMicroseconds (800);
}
}
void setup () {/ / The stepper motor used in the IO pin is set to output
pinMode (X_DIR, OUTPUT); pinMode (X_STP, OUTPUT);
pinMode (Y_DIR, OUTPUT); pinMode (Y_STP, OUTPUT);
pinMode (Z_DIR, OUTPUT); pinMode (Z_STP, OUTPUT);
pinMode (EN, OUTPUT);
digitalWrite (EN, LOW);
}
void loop () {
step (false, X_DIR, X_STP, 200); / / X axis motor reverse 1 ring, the 200 step is a circle.
step (false, Y_DIR, Y_STP, 200); / / y axis motor reverse 1 ring, the 200 step is a circle.
step (false, Z_DIR, Z_STP, 200); / / z axis motor reverse 1 ring, the 200 step is a circle.
delay (1000);
step (true, X_DIR, X_STP, 200); / / X axis motor forward 1 laps, the 200 step is a circle.
step (true, Y_DIR, Y_STP, 200); / / y axis motor forward 1 laps, the 200 step is a circle.
step (true, Z_DIR, Z_STP, 200); / / z axis motor forward 1 laps, the 200 step is a circle.
delay (1000);
}
Notice:
When inserting the A4988 module, must be careful not to insert opposite. Stepper motor wiring as follows:
2A, 2B is a group (red, green), 1A, 1B is a group (blue, yellow), if want to change direction, can be change the position of one group , for example 2A, 2B mutually exchanged